The 2019 financial year was a very successful one for Porsche. The sports car manufacturer traditionally allows its employees to share in the company's success. In times of the Corona crisis, the company is combining the voluntary bonus with an appeal for donations to its employees to support the "Porsche aid" program.
Read MoreFERRARI AND CLIENTS RAISE €1MILLION TO FIGHT THE COVID-19 PANDEMIC - IN AID OF MODENA'S HEALTHCARE SYSTEM
Maranello, 9 April 2020 – Ferrari's efforts to address the coronavirus pandemic continue: the Company has launched a fundraiser to support the health system of the province of Modena and will be matching all of the donations made by its clients.
Read MoreFerrari Announces The Suspension of Production in Maranello and Modena Until 3rd May 2020
Update Maranello, 27 March 2020 – Ferrari N.V. (“Ferrari” or the “Company”) (NYSE/MTA: RACE) announces today that subject to supply chain continuity it now plans to resume production as of 14 April 2020.
Read More#RaceHome, Audi e-tron Vision Gran Turismo
#RaceHome: DTM drivers from Audi in virtual races for a good cause
Audi factory driver Mike Rockenfeller has initiated a virtual racing series under the motto #RaceHome, which will be held on the PlayStation 4 with the fully-electric Audi e-tron Vision Gran Turismo. The proceeds will be used for a good cause. Once a week, fans of the Audi brand and SimRacing professionals will be competing against the six Audi DTM drivers: Loïc Duval, Jamie Green, Nico Müller, Robin Frijns, René Rast and Mike Rockenfeller.
Read MoreMcLAREN TECH CLUB: CONVERSATIONS ONLINE WITH THE MINDS BEHIND OUR PIONEERING TECHNOLOGIES
McLaren Tech Club (#McLarenTechClub) is designed for those who want to delve deeper into the core of every McLaren car while also increasing their automotive knowledge.
Read MoreROLLS-ROYCE CHALLENGES YOUNG MINDS TO DESIGN THEIR OWN LUXURY CAR
Rolls-Royce Motor Cars is a brand that encourages the pursuit of dreams, and now a new generation of aspiring designers are being encouraged to bring their automotive dreams to life through a special ‘Young Designer Competition’.
Read MoreBENTLEY'S IN-HOUSE METROLOGY TEAM UNDER THE MICROSCOPE
Deep in the heart of the Bentley factory in Crewe is a large, airy and air-conditioned workshop that visitors, even out of a government lockdown, will never see. It’s packed with the kind of precision instruments you’d expect to find in a space agency facility or university science lab. It’s here that Head of Metrology Michael Stockdale and his 25 colleagues measure every part of a Bentley to the highest standards of precision.
Read MoreGM to Make Face Masks for Frontline Workers
DETROIT – As the COVID-19 pandemic spread across the country, it created a critical shortage of face masks. To help protect workers in essential services across the country, GM launched a rapid-response project to produce masks at scale on Friday, March 20. Seven days later, the team had produced their first sample on the new production line.
By next week, GM expects to deliver its first 20,000 masks to frontline workers.
Without help from GM’s partners around the globe, the project would have taken several months to plan and execute. The team working on GM’s face-mask project accomplished the task in just one week.
“Our team began looking at ways we could quickly utilize our talents and resources to help in the shared fight against COVID-19,” said Peter Thom, GM vice president, Global Manufacturing Engineering. “Working around the clock, our team rallied with incredible passion and focus to come up with a plan to produce masks that will help protect the women and men on the front lines of this crisis.”
Project kickoff to first mask in six days, 23 hours, 30 minutes
At 3 p.m. on Friday, March 20, the core team assembled for the first time, kicking off the project and starting the timer.
“Because we wanted to move fast, the team set an incredibly aggressive goal: To have the production line up and running tests within a week,” said Thom.
More than 30 engineers, designers, buyers and members of the manufacturing team were asked to help with product development, sourcing materials and equipment, and planning the production process.
“The first people we called were those who work with fabric vehicle components,” said Karsten Garbe, GM plant director, Global Pre-Production Operations. “In a few days, the company’s seat belt and interior trim experts became experts in manufacturing face masks.”
The team sourced the necessary raw materials by leveraging GM’s existing supply chain. These materials include metal nose pieces, elastic straps and blown, non-woven fabric filter material. Simultaneously, GM collaborated with JR Automation in Holland, Michigan and Esys Automation in Auburn Hills to design and build the custom machinery needed to assemble the masks.
For the project, the team selected the ISO Class 8-equivalent cleanroom at GM’s manufacturing plant in Warren. Work began at the Warren facility by removing existing equipment from the cleanroom. The team cleared approximately 31,000 square feet to accommodate the mask production lines. Crews then installed new electrical service lines to power the production equipment and assembly stations.
With the site cleared and prepped, production equipment and materials were then delivered to the Warren facility. Crews worked around the clock to install equipment and stage the production line. The team then tested each step in the production process, looking for opportunities to improve quality and production speed.
At 2:30 p.m. on Friday, March 27, the project team had their first production-made mask in their hands.
“Not only did the team make their goal, but they over-delivered,” said Thom. “They actually beat our deadline, running the first mask through the equipment 30 minutes ahead of target. We’re excited because this means we’re even closer to being able to protect the healthcare teams who are working tirelessly to save lives.”
20,000 masks expected to be delivered on April 8
The projected production volume is just as aggressive as the project’s timeline. By Monday, March 30, more than 2,000 masks were produced by teams working through the weekend. These initial test samples will be used to ensure the quality standards are met. Once these quality measures are completed, the team expects to start producing masks for delivery early next week.
GM and the UAW will seek more than two dozen paid volunteers from Detroit-area plants to staff mask operations. In addition, GM has implemented a series of safety measures to protect these team members through physical distancing, enhanced on-site cleaning and pre-entry health screening.
The team expects to have 20,000 masks ready for delivery on Wednesday, April 8. Once the line is running at full speed, it will be able to produce up to 50,000 masks every day – or up to 1.5 million masks a month. GM is currently developing a plan for distributing the masks, including using some of this important safety equipment to protect employees in critical GM operations.
Navigating the Pandemic – A discussion with SEMA Members
Presenter Gene Marks and the SEMA member panelist group provide relevant information on how to navigate the COVID-19 challenges for individuals and businesses.
TESTING TIMES FOR THE NEW JEEP RENEGADE AND COMPASS 4XE IN ARJEPLOG
The Jeep Renegade and Compass 4xe herald a new era for the American brand and to mark this, Jeep had released videos shot as the new models completed an epic 3,800km road test from the Mirafiori plant in Turin to the Proving Ground in Arjeplog, Swedish Lapland.
Read MoreStrict Protocols in Place to Protect the Health of the GM Team Building Ventec’s Critical Care Ventilators in Kokomo
KOKOMO, Ind. – General Motors Co. (NYSE: GM) is actively training employees at the company’s Kokomo plant in the extensive screening, cleaning and other CDC-recommended procedures that will be in place when volume production of Ventec Life Systems’ critical care ventilator begins in less than two weeks. Among the employees is UAW Local 292 member Debbie Hollis of Kokomo.
Debbie Hollis
“I have family all across the country, so (COVID-19) has impacted everybody that I know and love,” Hollis said. “I’m grateful that I get a chance to do my part and be a part of something...we are modern-day Rosie the Riveters.”
Hollis and the production team, which will grow to more than 1,000 men and women, including people who already work for GM and new hires from the Kokomo area, are also gaining hands-on exposure to Ventec’s ventilator.
“Every ventilator we build can help save lives, and GM’s global supply base and manufacturing teams, the UAW, and the Kokomo community are working with passion and unwavering commitment to getting the job done,” said Gerald Johnson, GM executive vice president, Global Manufacturing. “People have moved mountains to help increase the production of Ventec’s critical care ventilator and we are just weeks away from delivering these lifesaving devices. I have never seen anything like it in my career.”
Kokomo Mayor Tyler Moore said his community is more than ready to do its part, “At this critical moment in our country’s battle against the COVID-19 pandemic, the Kokomo community applauds GM and Ventec leadership for joining the fight by producing much-needed medical ventilators here in their Kokomo facilities. At the same time, they have placed their trust in our community and the incredible Kokomo-area workforce. Kokomo is deeply honored to be a part of this extraordinary endeavor in these extraordinary times.”
Saving Lives and Keeping People Safe
To help protect people working at the Kokomo plant, extensive screening, cleaning, and other CDC-recommended procedures will be in place.
Arrival for Work:
Everyone arriving for work will be required to sanitize their hands immediately upon arrival and have their temperature checked with a non-contact thermometer before entering the job site.
Everyone will work their shift wearing medical-grade protective masks, including masks produced at GM’s Warren, Michigan facility.
At Work:
There will be a 30-minute interval between shifts to allow employees to clean their workstations when they arrive and again before they leave.
There will be signage throughout the facility reminding team members to practice social distancing.
Each workstation will be manned by one person, and each workstation will be spaced at least six feet apart.
Cleaning crews will clean and sanitize common touch surfaces such as door handles, as well as common areas, at least three times per shift.
Between Shifts:
Initial production will begin with one shift, with second and third shifts added soon thereafter.
Each shift will enter and exit through a different door to minimize social contact.
“The men and women building these ventilators raised their hands to help save the lives of people suffering from COVID-19,” said Dr. Jeffery E. Hess, GM corporate medical director. “We will create a safe workplace using CDC guidelines and scientific data.”
Strong Support from UAW Leadership
The health and safety of every person who enters a GM facility is the top priority for GM and the UAW, especially as people come together to meet the country’s need for ventilators.
“As our nation struggles with the COVID-19 pandemic, volunteer UAW-GM members are doing a tremendous service for our country by volunteering to come to work to make ventilators in Kokomo,” said Terry Dittes, vice president, UAW-GM Department. “For that reason, the UAW has worked with GM to put in place stringent CDC health and safety protocols. Our goal is to make sure that each and every day, people return home to their families and communities safe and healthy. We applaud their courage in volunteering in our nation’s time of need, and we commend GM for working with the UAW to save lives across this country.”
Added Greg Wohlford, UAW Local 292 shop chairperson, “Our members responded to the call for help with courage and a desire to help America save its citizens’ lives. We have pledged, along with GM, to do everything we can to make sure that we keep these everyday heroes safe from illness and injury. The UAW is excited about working with Ventec and GM to produce ventilators in Kokomo, Indiana.”
A Phone Call Sets an Unprecedented Effort into Motion
The unprecedented teamwork that has allowed ventilator production in Kokomo to move forward so quickly began with a March 17 phone call between General Motors Chairman and CEO Mary Barra and representatives of StopTheSpread.Org, who suggested GM work with Ventec.
StopTheSpread.org was founded by Kenneth Chenault, chairman and managing director at General Catalyst and the former chief executive and chairman of American Express, and Rachel Romer Carlson, the chief executive and co-founder of Guild Education.
GM and Ventec executives had their first conference call on Wednesday, March 18 to explore how GM may be able to help Ventec increase ventilator production.
The next day, a GM team flew to Seattle to meet with the Ventec team and roll up their sleeves to help.
On Friday, March 20, GM engaged its global supply base and within 72 hours, they had developed plans to source 100 percent of the necessary parts.
The UAW’s national and local leadership embraced the project and on Wednesday, March 25, crews began preparing the Kokomo site for production.
Mass production begins in mid-April. Production will quickly scale up to 10,000 critical care ventilators or more per month.
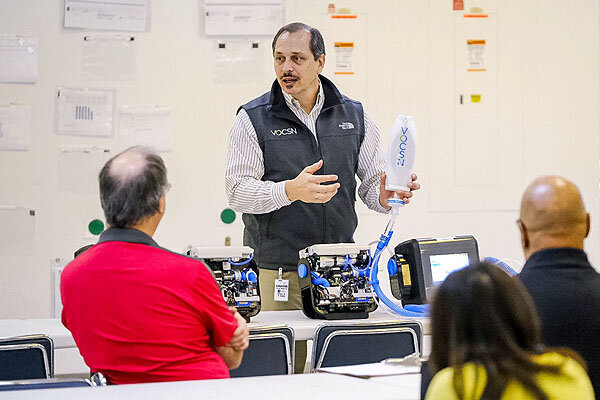
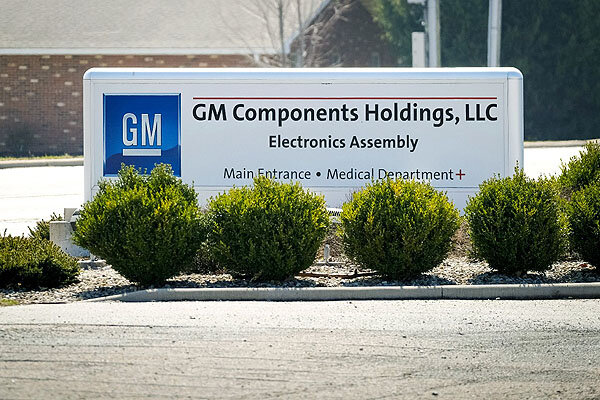
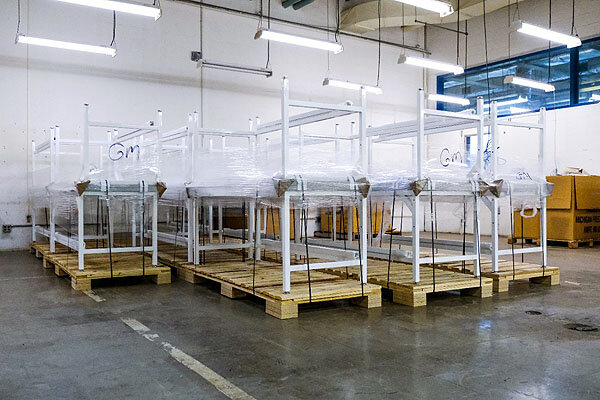
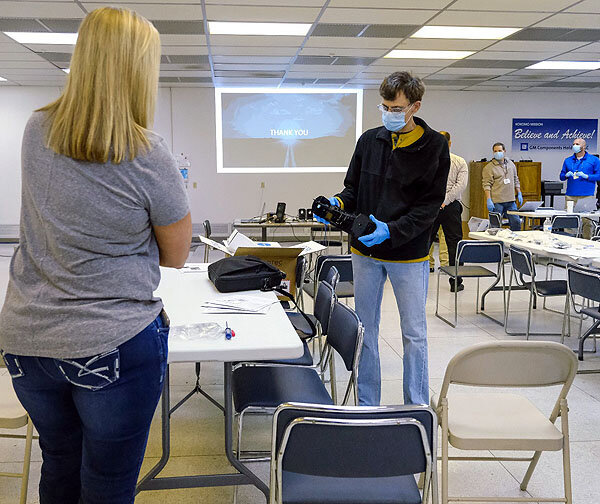
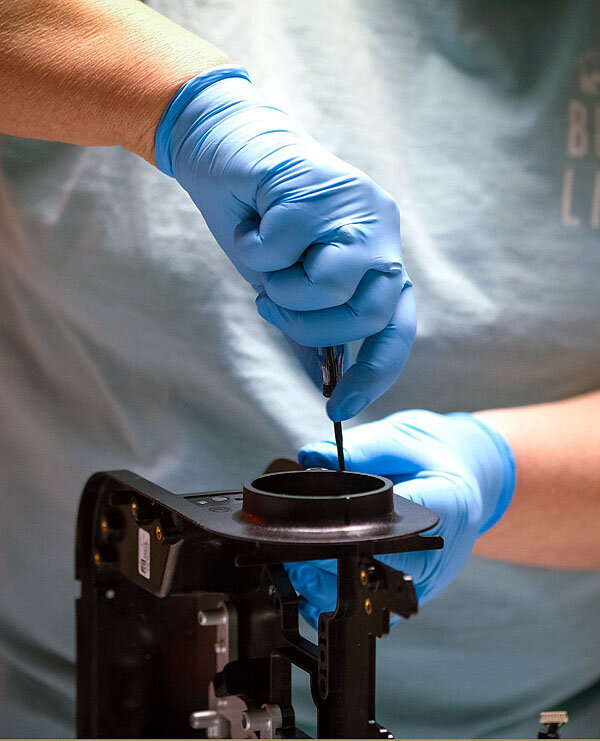
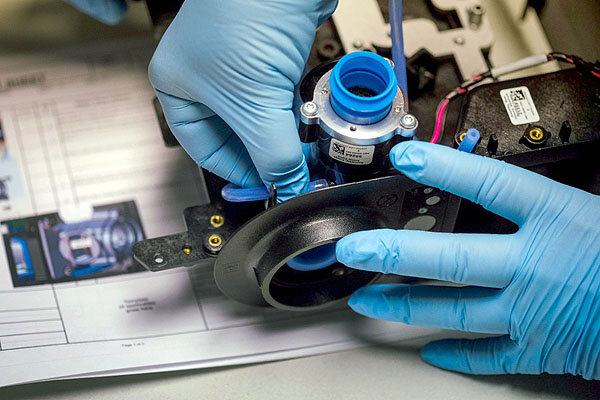
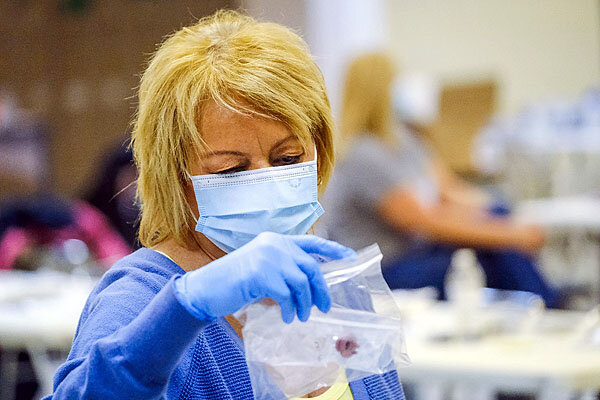
BMW Group reaffirms its ongoing commitment to hydrogen fuel cell technology.
Munich. Developing alternative powertrain technologies is a top priority for the BMW Group. The premium carmaker offers first virtual insights into the powertrain system for the BMW i Hydrogen NEXT and reaffirms s its commitment to following a carefully considered and systematic route to emission-free mobility. This approach also includes the careful consideration of different market and customer requirements as part of the company’s Power of Choice strategy. Customer centricity and the flexibility needed for this are essential in facilitating the breakthrough for sustainable mobility on the global stage.
Read More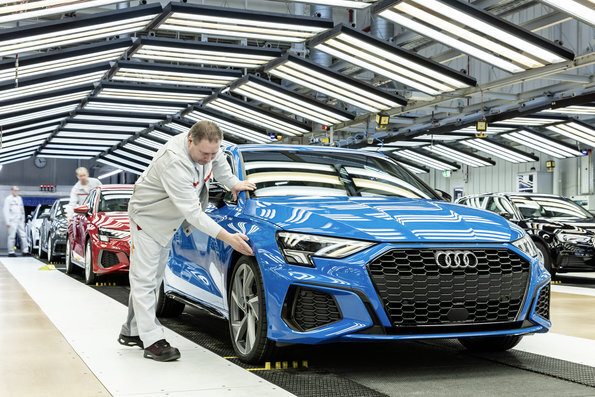
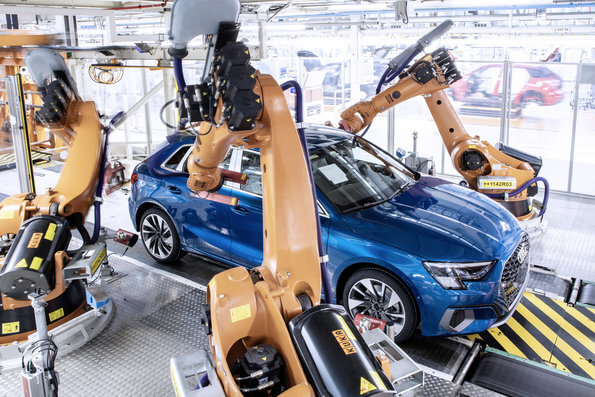
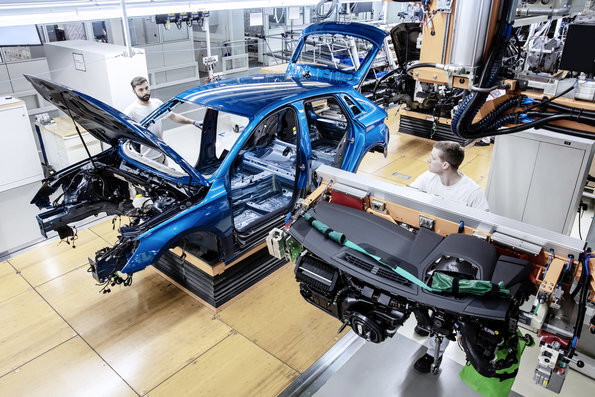
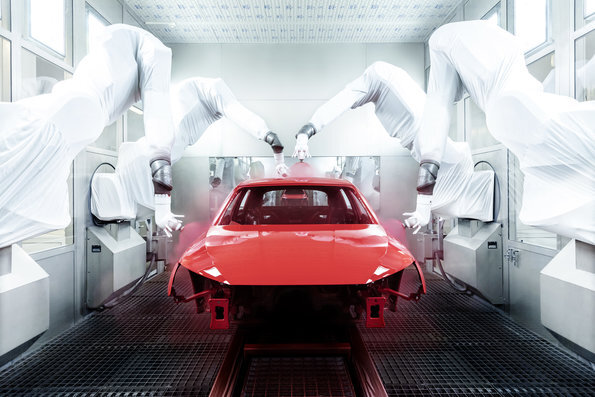
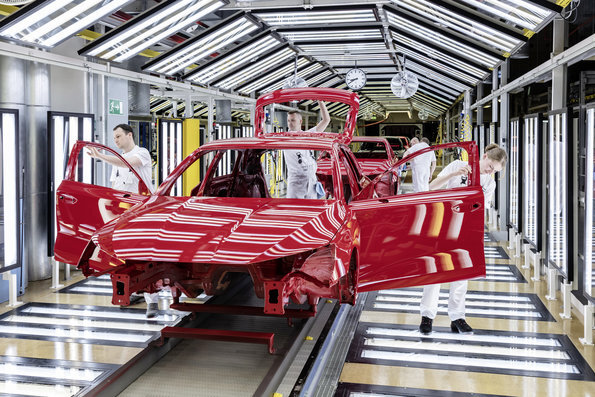
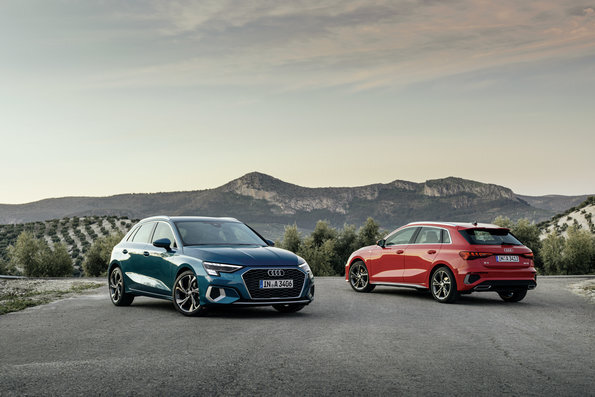
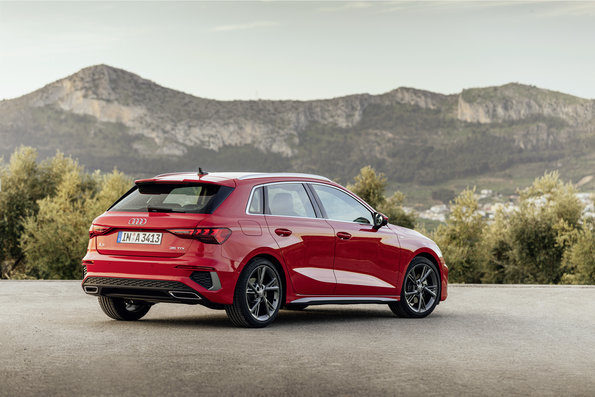
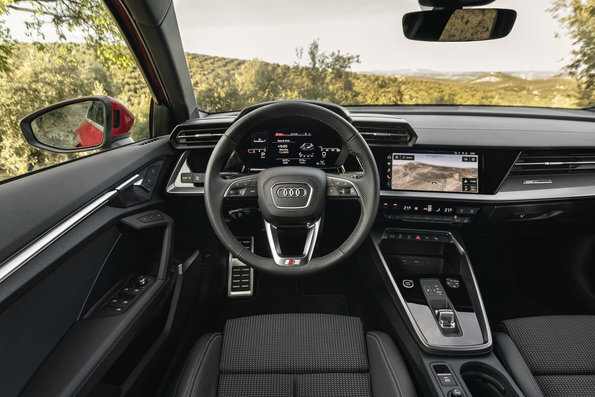
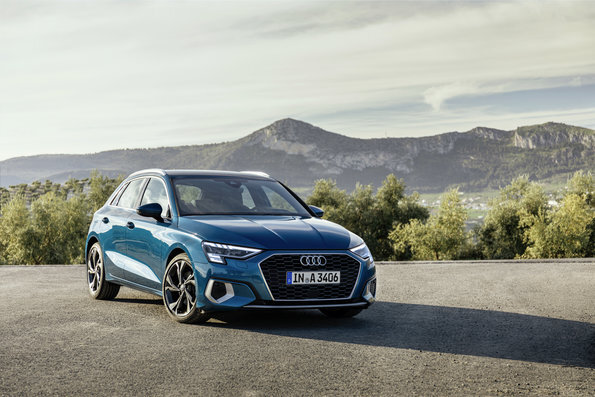
Start of production of the new Audi A3 Sportback in Ingolstadt
The Audi A3 is a successful model: Today, Plant Manager Achim Heinfling unveiled the new, eagerly awaited fourth A3 generation in front of employees in the Audi Forum in Ingolstadt on the occasion of the world premiere of the new premium compact.
Read MoreBugatti EB110, Veyron, Chiron – The Holy Trinity of modern Bugatti
All-wheel-drive, four turbochargers and a monocoque made of carbon – Bugatti’s proven and continuously improved ingredients for super sports cars from the last three decades. The Bugatti EB110, Veyron and Chiron1 are seen as milestones in automotive engineering from the 1990s, 2000s, and 2010s. Bugatti enthusiasts and owners worldwide dream of having all three vehicles complete in their own collection as the “Holy Trinity of modern Bugatti”. They are both coveted collector’s items and investments. All three models came together for a photoshoot – unique photos of a collection that rarely exists in the world.
Read MoreThe Master Craftspeople Behind 'The Grand Bentley'
After nearly a decade as Bentley’s flagship model, the Mulsanne will soon complete its production run and pass its torch to the all-new Flying Spur. Before then, and while the factory is shut down due to the ongoing global crisis, Bentley is celebrating the unmatched skills and expertise of the master craftspeople behind the ultimate luxury sedan. Production of the Mulsanne was due to finish in April but has now been extended so that the final cars will be handcrafted when the Bentley workforce returns to the Crewe factory after the COVID-19 crisis.
Read MoreFCA STRIKES A POSE WITH ON-TREND ACCESSORIES CAMPAIGN: GET THE 2020 LOOK
Customers looking to refresh and enhance the look and feel of their car need to look no further than MOPAR’s new authentic accessories campaign ‘GET THE 2020 LOOK’.
Read More