Today, General Motors announced the opening of the 15,000-square-foot Additive Industrialization Center, a ground-up facility exclusively dedicated to productionizing 3D printing technology in the automotive industry. The AIC is the capstone of GM’s expertise and increased investment in 3D printing over the last several years.
Read MoreSTUDIES SHOW GM BUILDS THE MOST AMERICAN-MADE VEHICLE MODELS
In the Cars.com annual American-Made Index for 2020, nine of the top 25 models are GM products, more than any other manufacturer. The Cars.com report ranked 91 models assembled in the U.S. for the 2020 model year, rating them across several factors, including a percentage of U.S. and Canadian parts; country of origin for available engines; country of origin for available transmissions; and U.S. manufacturing employees relative to the automaker’s footprint.
Read MoreGeneral Motors Statement on its Petition for a Writ of Mandamus in RICO Lawsuit Against FCA and Other Defendants
General Motors has played a vital role in helping the country fight the COVID-19 pandemic, advance diversity, and inclusion, and drive prosperity with good-paying jobs. Nothing, including the RICO lawsuit we filed against FCA and three convicted former FCA executives, has or will distract GM and its leadership team from “fully providing their vision and leadership” on these critical issues now and into the future. And we reject the notion that seeking justice for the direct harm caused to GM is a “waste of time,” a “distraction” or a “diversion.” Justice is worth pursuing in all its facets and any forums.
Read MoreGM Defense Awarded a $214.3M Contract to Produce the U.S. Army’s Infantry Squad Vehicle
U.S. Army has awarded GM Defense LLC, $214.3M production contract to build, field, and sustain the Army’s new Infantry Squad Vehicle (ISV). GM Defense’s solution to the Army’s next-generation transportation needs is based on the award-winning 2020 Chevrolet Colorado ZR2 midsize truck architecture and leverages 90 percent commercial-off-the-shelf parts.
Read MoreGM to Make Face Masks for Frontline Workers
DETROIT – As the COVID-19 pandemic spread across the country, it created a critical shortage of face masks. To help protect workers in essential services across the country, GM launched a rapid-response project to produce masks at scale on Friday, March 20. Seven days later, the team had produced their first sample on the new production line.
By next week, GM expects to deliver its first 20,000 masks to frontline workers.
Without help from GM’s partners around the globe, the project would have taken several months to plan and execute. The team working on GM’s face-mask project accomplished the task in just one week.
“Our team began looking at ways we could quickly utilize our talents and resources to help in the shared fight against COVID-19,” said Peter Thom, GM vice president, Global Manufacturing Engineering. “Working around the clock, our team rallied with incredible passion and focus to come up with a plan to produce masks that will help protect the women and men on the front lines of this crisis.”
Project kickoff to first mask in six days, 23 hours, 30 minutes
At 3 p.m. on Friday, March 20, the core team assembled for the first time, kicking off the project and starting the timer.
“Because we wanted to move fast, the team set an incredibly aggressive goal: To have the production line up and running tests within a week,” said Thom.
More than 30 engineers, designers, buyers and members of the manufacturing team were asked to help with product development, sourcing materials and equipment, and planning the production process.
“The first people we called were those who work with fabric vehicle components,” said Karsten Garbe, GM plant director, Global Pre-Production Operations. “In a few days, the company’s seat belt and interior trim experts became experts in manufacturing face masks.”
The team sourced the necessary raw materials by leveraging GM’s existing supply chain. These materials include metal nose pieces, elastic straps and blown, non-woven fabric filter material. Simultaneously, GM collaborated with JR Automation in Holland, Michigan and Esys Automation in Auburn Hills to design and build the custom machinery needed to assemble the masks.
For the project, the team selected the ISO Class 8-equivalent cleanroom at GM’s manufacturing plant in Warren. Work began at the Warren facility by removing existing equipment from the cleanroom. The team cleared approximately 31,000 square feet to accommodate the mask production lines. Crews then installed new electrical service lines to power the production equipment and assembly stations.
With the site cleared and prepped, production equipment and materials were then delivered to the Warren facility. Crews worked around the clock to install equipment and stage the production line. The team then tested each step in the production process, looking for opportunities to improve quality and production speed.
At 2:30 p.m. on Friday, March 27, the project team had their first production-made mask in their hands.
“Not only did the team make their goal, but they over-delivered,” said Thom. “They actually beat our deadline, running the first mask through the equipment 30 minutes ahead of target. We’re excited because this means we’re even closer to being able to protect the healthcare teams who are working tirelessly to save lives.”
20,000 masks expected to be delivered on April 8
The projected production volume is just as aggressive as the project’s timeline. By Monday, March 30, more than 2,000 masks were produced by teams working through the weekend. These initial test samples will be used to ensure the quality standards are met. Once these quality measures are completed, the team expects to start producing masks for delivery early next week.
GM and the UAW will seek more than two dozen paid volunteers from Detroit-area plants to staff mask operations. In addition, GM has implemented a series of safety measures to protect these team members through physical distancing, enhanced on-site cleaning and pre-entry health screening.
The team expects to have 20,000 masks ready for delivery on Wednesday, April 8. Once the line is running at full speed, it will be able to produce up to 50,000 masks every day – or up to 1.5 million masks a month. GM is currently developing a plan for distributing the masks, including using some of this important safety equipment to protect employees in critical GM operations.
Strict Protocols in Place to Protect the Health of the GM Team Building Ventec’s Critical Care Ventilators in Kokomo
KOKOMO, Ind. – General Motors Co. (NYSE: GM) is actively training employees at the company’s Kokomo plant in the extensive screening, cleaning and other CDC-recommended procedures that will be in place when volume production of Ventec Life Systems’ critical care ventilator begins in less than two weeks. Among the employees is UAW Local 292 member Debbie Hollis of Kokomo.
Debbie Hollis
“I have family all across the country, so (COVID-19) has impacted everybody that I know and love,” Hollis said. “I’m grateful that I get a chance to do my part and be a part of something...we are modern-day Rosie the Riveters.”
Hollis and the production team, which will grow to more than 1,000 men and women, including people who already work for GM and new hires from the Kokomo area, are also gaining hands-on exposure to Ventec’s ventilator.
“Every ventilator we build can help save lives, and GM’s global supply base and manufacturing teams, the UAW, and the Kokomo community are working with passion and unwavering commitment to getting the job done,” said Gerald Johnson, GM executive vice president, Global Manufacturing. “People have moved mountains to help increase the production of Ventec’s critical care ventilator and we are just weeks away from delivering these lifesaving devices. I have never seen anything like it in my career.”
Kokomo Mayor Tyler Moore said his community is more than ready to do its part, “At this critical moment in our country’s battle against the COVID-19 pandemic, the Kokomo community applauds GM and Ventec leadership for joining the fight by producing much-needed medical ventilators here in their Kokomo facilities. At the same time, they have placed their trust in our community and the incredible Kokomo-area workforce. Kokomo is deeply honored to be a part of this extraordinary endeavor in these extraordinary times.”
Saving Lives and Keeping People Safe
To help protect people working at the Kokomo plant, extensive screening, cleaning, and other CDC-recommended procedures will be in place.
Arrival for Work:
Everyone arriving for work will be required to sanitize their hands immediately upon arrival and have their temperature checked with a non-contact thermometer before entering the job site.
Everyone will work their shift wearing medical-grade protective masks, including masks produced at GM’s Warren, Michigan facility.
At Work:
There will be a 30-minute interval between shifts to allow employees to clean their workstations when they arrive and again before they leave.
There will be signage throughout the facility reminding team members to practice social distancing.
Each workstation will be manned by one person, and each workstation will be spaced at least six feet apart.
Cleaning crews will clean and sanitize common touch surfaces such as door handles, as well as common areas, at least three times per shift.
Between Shifts:
Initial production will begin with one shift, with second and third shifts added soon thereafter.
Each shift will enter and exit through a different door to minimize social contact.
“The men and women building these ventilators raised their hands to help save the lives of people suffering from COVID-19,” said Dr. Jeffery E. Hess, GM corporate medical director. “We will create a safe workplace using CDC guidelines and scientific data.”
Strong Support from UAW Leadership
The health and safety of every person who enters a GM facility is the top priority for GM and the UAW, especially as people come together to meet the country’s need for ventilators.
“As our nation struggles with the COVID-19 pandemic, volunteer UAW-GM members are doing a tremendous service for our country by volunteering to come to work to make ventilators in Kokomo,” said Terry Dittes, vice president, UAW-GM Department. “For that reason, the UAW has worked with GM to put in place stringent CDC health and safety protocols. Our goal is to make sure that each and every day, people return home to their families and communities safe and healthy. We applaud their courage in volunteering in our nation’s time of need, and we commend GM for working with the UAW to save lives across this country.”
Added Greg Wohlford, UAW Local 292 shop chairperson, “Our members responded to the call for help with courage and a desire to help America save its citizens’ lives. We have pledged, along with GM, to do everything we can to make sure that we keep these everyday heroes safe from illness and injury. The UAW is excited about working with Ventec and GM to produce ventilators in Kokomo, Indiana.”
A Phone Call Sets an Unprecedented Effort into Motion
The unprecedented teamwork that has allowed ventilator production in Kokomo to move forward so quickly began with a March 17 phone call between General Motors Chairman and CEO Mary Barra and representatives of StopTheSpread.Org, who suggested GM work with Ventec.
StopTheSpread.org was founded by Kenneth Chenault, chairman and managing director at General Catalyst and the former chief executive and chairman of American Express, and Rachel Romer Carlson, the chief executive and co-founder of Guild Education.
GM and Ventec executives had their first conference call on Wednesday, March 18 to explore how GM may be able to help Ventec increase ventilator production.
The next day, a GM team flew to Seattle to meet with the Ventec team and roll up their sleeves to help.
On Friday, March 20, GM engaged its global supply base and within 72 hours, they had developed plans to source 100 percent of the necessary parts.
The UAW’s national and local leadership embraced the project and on Wednesday, March 25, crews began preparing the Kokomo site for production.
Mass production begins in mid-April. Production will quickly scale up to 10,000 critical care ventilators or more per month.
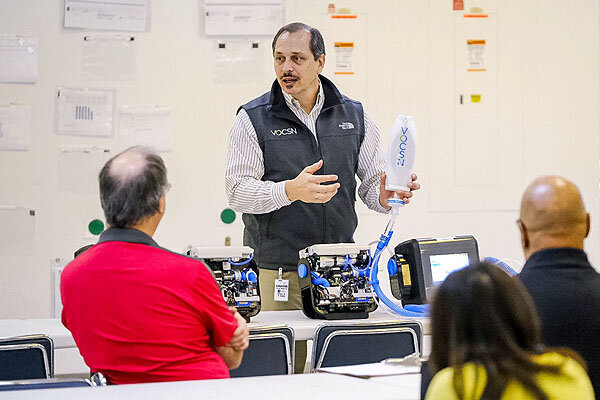
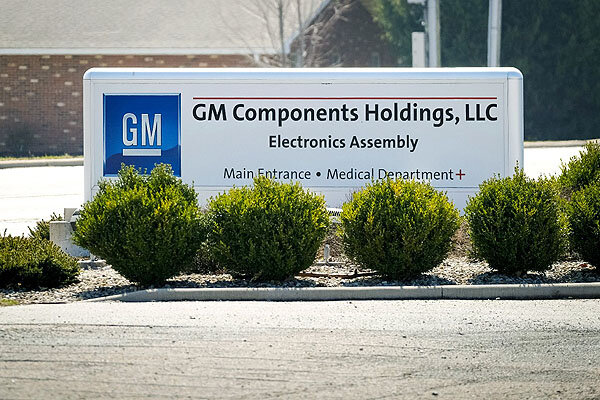
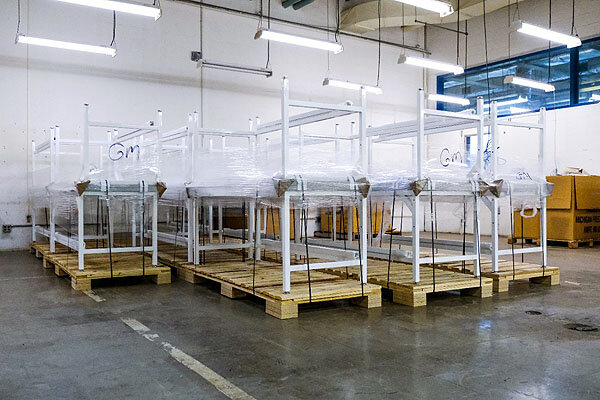
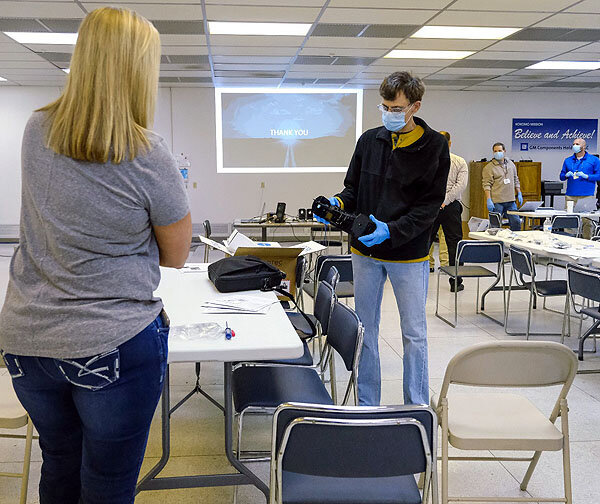
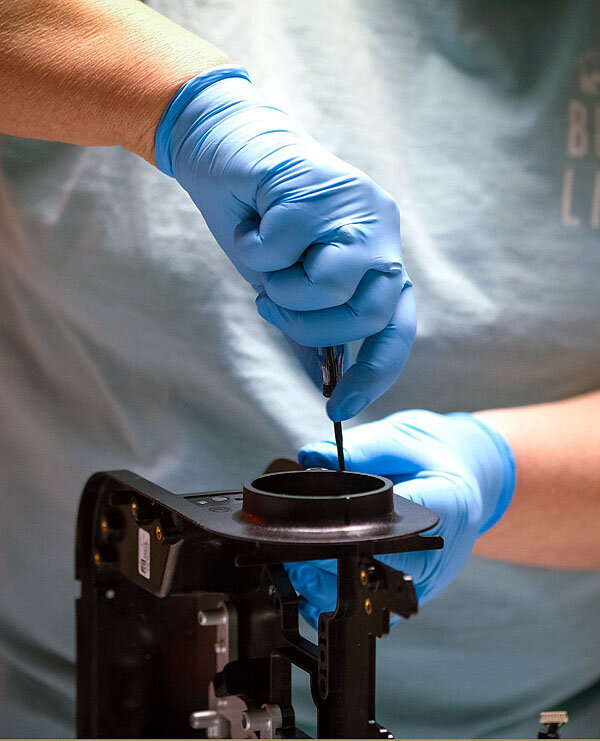
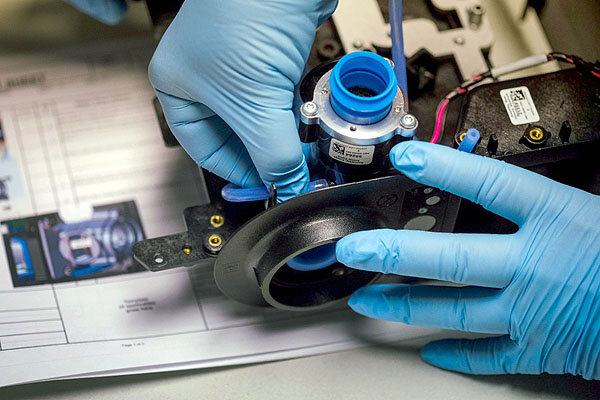
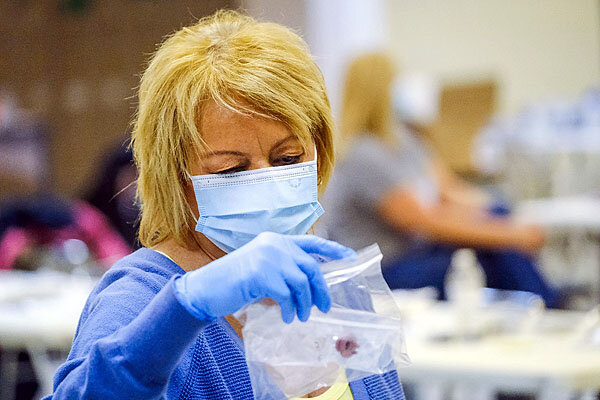
Mary Barra, GM chairman and CEO
GM Reveals New Ultium Batteries and a Flexible Global Platform to Rapidly Grow its EV Portfolio
WARREN, Mich. – Starting today, General Motors Co. (NYSE: GM) is gathering hundreds of employees, dealers, investors, analysts, media and policymakers to share details of its strategy to grow the company’s electric vehicle (EV) sales quickly, efficiently and profitably.
“Our team accepted the challenge to transform product development at GM and position our company for an all-electric future,” said Mary Barra, GM chairman, and CEO. “What we have done is build a multi-brand, multi-segment EV strategy with economies of scale that rival our full-size truck business with much less complexity and even more flexibility.”
The heart of GM’s strategy is a modular propulsion system and a highly flexible, third-generation global EV platform powered by proprietary Ultium batteries. They will allow the company to compete for nearly every customer in the market today, whether they are looking for affordable transportation, a luxury experience, work trucks or a high-performance machine.
GM President Mark Reuss
“Thousands of GM scientists, engineers and designers are working to execute a historic reinvention of the company,” said GM President Mark Reuss. “They are on the cusp of delivering a profitable EV business that can satisfy millions of customers.”
Ultium Batteries and Propulsion System Highlights
GM’s new Ultium batteries are unique in the industry because the large-format, pouch-style cells can be stacked vertically or horizontally inside the battery pack. This allows engineers to optimize battery energy storage and layout for each vehicle design.
Ultium energy options range from 50 to 200 kWh, which could enable a GM-estimated range up to 400 miles or more on a full charge with 0 to 60 mph acceleration as low as 3 seconds. Motors designed in-house will support front-wheel drive, rear-wheel drive, all-wheel drive, and performance all-wheel drive applications.
Ultium-powered EVs are designed for Level 2 and DC fast charging. Most will have 400-volt battery packs and up to 200kW fast-charging capability while our truck platform will have 800-volt battery packs and 350 kW fast-charging capability.
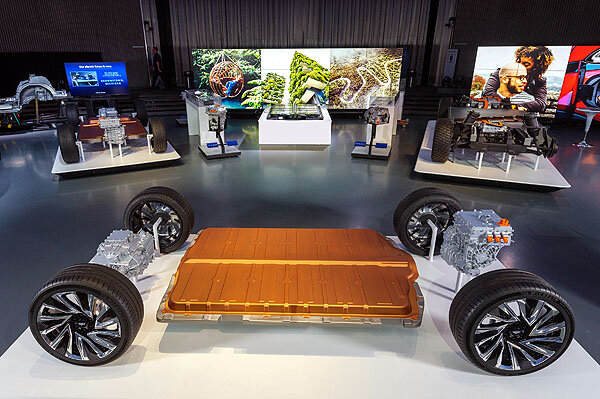
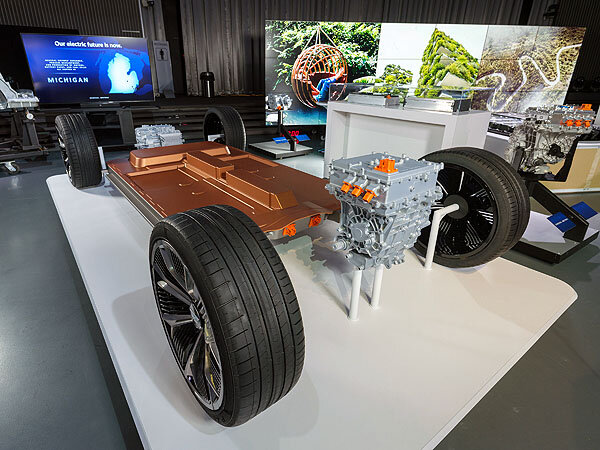
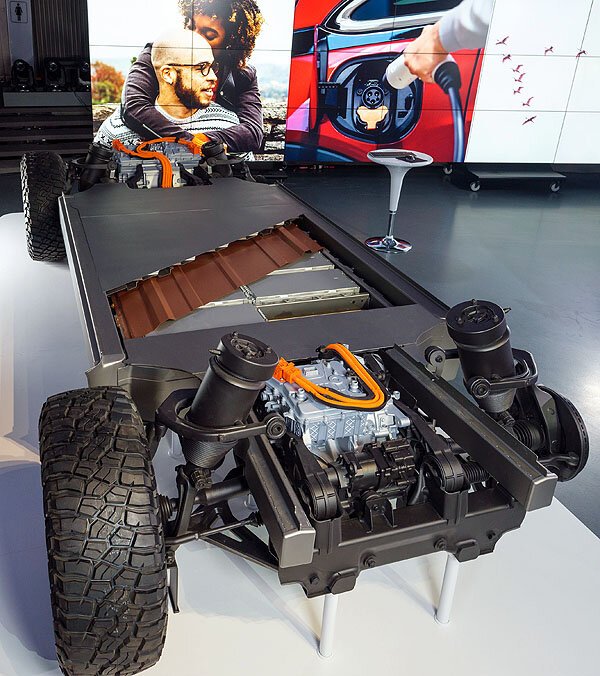
GM’s flexible, modular approach to EV development will drive significant economies of scale and create new revenue opportunities, including:
Continuous Improvement in Battery Costs: GM’s joint venture with LG Chem will drive battery cell costs below $100/kWh. The cells use a proprietary low cobalt chemistry and ongoing technological and manufacturing breakthroughs will drive costs even lower.
Flexibility: GM’s all-new global platform is flexible enough to build a wide range of trucks, SUVs, crossovers, cars and commercial vehicles with outstanding design, performance, packaging, range, and affordability.
Capital Efficiency: GM can spend less capital to scale its EV business because it is able to leverage existing property, including land, buildings, tools and production equipment such as body shops and paint shops.
Complexity Reduction: The vehicle and propulsion systems were designed together to minimize complexity and part counts beyond today’s EVs, which are less complex than conventional vehicles powered by internal combustion engines. For example, GM plans 19 different battery and drive unit configurations initially, compared with 550 internal combustion powertrain combinations available today.
Rising Customer Acceptance: Third-party forecasters expect U.S. EV volumes to more than double from 2025 to 2030 to about 3 million units on average. GM believes volumes could be materially higher as more EVs are launched in popular segments, charging networks grow and the total cost of ownership to consumers continues to fall.
New Sources of Revenue: By vertically integrating the manufacture of battery cells, the company can reach beyond its own fleet and license the technology to others.