Goodguys Rod & Custom Association, the organizer of America's premier hot rod and custom car events, has announced that Kahn Media will exclusively represent the automotive event producer as its Agency of Record. Kahn Media will use its public relations, social media, and digital marketing expertise to expand consumer awareness of the Goodguys organization and the 19 events it is hosting around the United States in 2021.
Read MoreNew Pathogen-Pumppelling Product Promises Peace of Mind for Motor Trade & Fleet Sectors as Vehicle Hygiene Becomes a Top Priority
As businesses look to return after the impact of the COVID-19 crisis, a new off-the-shelf product that can sterilize a vehicle interior in a matter of minutes is set to revolutionize the fleet, vehicle rental, and used car trade.
Sany Car is a portable device that uses ozone gas to sanitize vehicles in minutes, with a cost per treatment as low as £0.93 per vehicle. Used by businesses across Europe and endorsed by many car manufacturers, it has the backing of the Red Cross as well as national police forces and authorities.
Read MoreNew Luxury Silk Face Masks, From The Outlierman, Handcrafted in Como, Italy
The Outlierman, makers of handcrafted luxury automotive-inspired accessories, has reopened for the first time since the COVID-19 pandemic with the release of a beautifully designed collection of non-medical face coverings, featuring some of the company’s most popular automotive designs.
Read MoreFORD QUICK TO MANUFACTURE VENTILATORS FOR UK’S NATIONAL HEALTH SERVICE
Ford is making ventilator sub-assemblies for the National Health Service (NHS) in the UK after transforming an empty warehouse into a manufacturing facility in record time.
Employees worked ceaselessly for three weeks to get the high-tech production line up and running – a feat that would usually take a full year. The facility is part of the VentilatorChallengeUK Consortium – a collaboration between leading tech and engineering companies to deliver 15,000 much-needed Penlon Prima ES02 ventilators that the NHS will use for critically ill COVID-19 patients.
Read MoreBENTLEY LEADS THREE RACE SERIES AFTER OPENING ROUNDS
Bentley Motorsport’s squad of elite works racing drivers have commenced three-race series in 2020 – the Intercontinental GT Challenge, SRO E-Sport GT Series, and The Race All-Star Series - and, after the opening round of each, they are leading them all.
Read MoreAirlift for medical protective equipment
Business and politics are working closely together: Porsche, DB Schenker, and Lufthansa Cargo are helping Baden-Württemberg and the Free State of Saxony to overcome the coronavirus crisis.
For this purpose, the sports car manufacturer has put together a task force with six employees from the Procurement department and is organizing the supply chains of urgently needed protective equipment in China on behalf of the state governments.
Read MoreASTON MARTIN RACING TO MAKE ESPORTS DEBUT
Friday 1 May, 2020, Gaydon: Aston Martin will make its official debut in the esports arena this weekend, as it enters season two of The Race All-Star Series - beginning a five-week battle for the Pro Cup teams’ and drivers’ championships with three of its works drivers. It will also campaign for Legends Trophy honours with three-times Le Mans-winner Darren Turner.
Read MoreThe company’s operating result fell by 34 percent at €0.6 billion as compared to the previous year. The return on sales was 9.5 percent. Deliveries were down by 5 percent. The company handed over 53,125 vehicles to customers by the end of March. Since the beginning of the year, the workforce grew by one percent to 35,866 employees.
Porsche: Profits dip comparatively moderately
The company’s operating result fell by 34 percent at €0.6 billion as compared to the previous year. The return on sales was 9.5 percent. Deliveries were down by 5 percent. The company handed over 53,125 vehicles to customers by the end of March. Since the beginning of the year, the workforce grew by one percent to 35,866 employees.
Read MorePorsche is manufacturing sports cars again
As from next Monday (4 May), Porsche is restarting production on a site- and task-specific basis. All the required measures have been taken in advance to guarantee the maximum possible safety for employees and so that production can be increased in stages up to full capacity.
Read More#raceagainstCOVID: Ducati launches a fundraiser to support the Policlinico di S.Orsola Hospital in Bologna
Borgo Panigale (Bologna, Italy), May 4, 2020 - Ducati launches #raceagainstCovid, a fundraiser organized by the Borgo Panigale company in favor of the Policlinico di S.Orsola of Bologna, an excellence of the area as well as one of the largest hospitals in Italy. In this way, Ducati wishes to contribute to the fight against COVID-19, and it does so with the approach that most distinguishes the company - that of great challenges, forming a team, sharing a goal, and looking to the future.
Read MoreCustom Builder Rick Dore's The Illusion at The Quail, A Motorsports Gathering 2019 Photo by: Adam Swords Photography
The Quail, A Motorsports Gathering, The Peninsula Hotels Signature Motoring Event, has been suspended for 2020
The Quail, A Motorsports Gathering announced today that the 2020 edition of the world-class motoring event will be suspended in response to the ongoing COVID-19 situation.
Read MoreBugatti working from home – Design Director Achim Anscheidt
Long telephone conferences and many hours in front of a computer screen. Far away from the extraordinary hyper sports cars themselves. Bugatti has suspended the production of its vehicles such as the Chiron1 and Divo2 in Molsheim. Even so, many staff is continuing to work from home now, taking into account the recommendations of the respective authorities, international experts, and government measures. Like Achim Anscheidt, Bugatti’s Design Director since 2004.
Read MoreDelivery of computer equipment to the schools in Maranello
FERRARI COMES TO THE AID OF LOCAL COMMUNITIES
In response to the healthcare crisis caused by the COVID-19 pandemic, Ferrari has agreed to donate all or part of their annual compensation to fund a series of initiatives in the region with the first activities concentrating on the immediate communities of Maranello, Fiorano, and Formigine.
Read MoreGM to Make Face Masks for Frontline Workers
DETROIT – As the COVID-19 pandemic spread across the country, it created a critical shortage of face masks. To help protect workers in essential services across the country, GM launched a rapid-response project to produce masks at scale on Friday, March 20. Seven days later, the team had produced their first sample on the new production line.
By next week, GM expects to deliver its first 20,000 masks to frontline workers.
Without help from GM’s partners around the globe, the project would have taken several months to plan and execute. The team working on GM’s face-mask project accomplished the task in just one week.
“Our team began looking at ways we could quickly utilize our talents and resources to help in the shared fight against COVID-19,” said Peter Thom, GM vice president, Global Manufacturing Engineering. “Working around the clock, our team rallied with incredible passion and focus to come up with a plan to produce masks that will help protect the women and men on the front lines of this crisis.”
Project kickoff to first mask in six days, 23 hours, 30 minutes
At 3 p.m. on Friday, March 20, the core team assembled for the first time, kicking off the project and starting the timer.
“Because we wanted to move fast, the team set an incredibly aggressive goal: To have the production line up and running tests within a week,” said Thom.
More than 30 engineers, designers, buyers and members of the manufacturing team were asked to help with product development, sourcing materials and equipment, and planning the production process.
“The first people we called were those who work with fabric vehicle components,” said Karsten Garbe, GM plant director, Global Pre-Production Operations. “In a few days, the company’s seat belt and interior trim experts became experts in manufacturing face masks.”
The team sourced the necessary raw materials by leveraging GM’s existing supply chain. These materials include metal nose pieces, elastic straps and blown, non-woven fabric filter material. Simultaneously, GM collaborated with JR Automation in Holland, Michigan and Esys Automation in Auburn Hills to design and build the custom machinery needed to assemble the masks.
For the project, the team selected the ISO Class 8-equivalent cleanroom at GM’s manufacturing plant in Warren. Work began at the Warren facility by removing existing equipment from the cleanroom. The team cleared approximately 31,000 square feet to accommodate the mask production lines. Crews then installed new electrical service lines to power the production equipment and assembly stations.
With the site cleared and prepped, production equipment and materials were then delivered to the Warren facility. Crews worked around the clock to install equipment and stage the production line. The team then tested each step in the production process, looking for opportunities to improve quality and production speed.
At 2:30 p.m. on Friday, March 27, the project team had their first production-made mask in their hands.
“Not only did the team make their goal, but they over-delivered,” said Thom. “They actually beat our deadline, running the first mask through the equipment 30 minutes ahead of target. We’re excited because this means we’re even closer to being able to protect the healthcare teams who are working tirelessly to save lives.”
20,000 masks expected to be delivered on April 8
The projected production volume is just as aggressive as the project’s timeline. By Monday, March 30, more than 2,000 masks were produced by teams working through the weekend. These initial test samples will be used to ensure the quality standards are met. Once these quality measures are completed, the team expects to start producing masks for delivery early next week.
GM and the UAW will seek more than two dozen paid volunteers from Detroit-area plants to staff mask operations. In addition, GM has implemented a series of safety measures to protect these team members through physical distancing, enhanced on-site cleaning and pre-entry health screening.
The team expects to have 20,000 masks ready for delivery on Wednesday, April 8. Once the line is running at full speed, it will be able to produce up to 50,000 masks every day – or up to 1.5 million masks a month. GM is currently developing a plan for distributing the masks, including using some of this important safety equipment to protect employees in critical GM operations.
Navigating the Pandemic – A discussion with SEMA Members
Presenter Gene Marks and the SEMA member panelist group provide relevant information on how to navigate the COVID-19 challenges for individuals and businesses.
Strict Protocols in Place to Protect the Health of the GM Team Building Ventec’s Critical Care Ventilators in Kokomo
KOKOMO, Ind. – General Motors Co. (NYSE: GM) is actively training employees at the company’s Kokomo plant in the extensive screening, cleaning and other CDC-recommended procedures that will be in place when volume production of Ventec Life Systems’ critical care ventilator begins in less than two weeks. Among the employees is UAW Local 292 member Debbie Hollis of Kokomo.
Debbie Hollis
“I have family all across the country, so (COVID-19) has impacted everybody that I know and love,” Hollis said. “I’m grateful that I get a chance to do my part and be a part of something...we are modern-day Rosie the Riveters.”
Hollis and the production team, which will grow to more than 1,000 men and women, including people who already work for GM and new hires from the Kokomo area, are also gaining hands-on exposure to Ventec’s ventilator.
“Every ventilator we build can help save lives, and GM’s global supply base and manufacturing teams, the UAW, and the Kokomo community are working with passion and unwavering commitment to getting the job done,” said Gerald Johnson, GM executive vice president, Global Manufacturing. “People have moved mountains to help increase the production of Ventec’s critical care ventilator and we are just weeks away from delivering these lifesaving devices. I have never seen anything like it in my career.”
Kokomo Mayor Tyler Moore said his community is more than ready to do its part, “At this critical moment in our country’s battle against the COVID-19 pandemic, the Kokomo community applauds GM and Ventec leadership for joining the fight by producing much-needed medical ventilators here in their Kokomo facilities. At the same time, they have placed their trust in our community and the incredible Kokomo-area workforce. Kokomo is deeply honored to be a part of this extraordinary endeavor in these extraordinary times.”
Saving Lives and Keeping People Safe
To help protect people working at the Kokomo plant, extensive screening, cleaning, and other CDC-recommended procedures will be in place.
Arrival for Work:
Everyone arriving for work will be required to sanitize their hands immediately upon arrival and have their temperature checked with a non-contact thermometer before entering the job site.
Everyone will work their shift wearing medical-grade protective masks, including masks produced at GM’s Warren, Michigan facility.
At Work:
There will be a 30-minute interval between shifts to allow employees to clean their workstations when they arrive and again before they leave.
There will be signage throughout the facility reminding team members to practice social distancing.
Each workstation will be manned by one person, and each workstation will be spaced at least six feet apart.
Cleaning crews will clean and sanitize common touch surfaces such as door handles, as well as common areas, at least three times per shift.
Between Shifts:
Initial production will begin with one shift, with second and third shifts added soon thereafter.
Each shift will enter and exit through a different door to minimize social contact.
“The men and women building these ventilators raised their hands to help save the lives of people suffering from COVID-19,” said Dr. Jeffery E. Hess, GM corporate medical director. “We will create a safe workplace using CDC guidelines and scientific data.”
Strong Support from UAW Leadership
The health and safety of every person who enters a GM facility is the top priority for GM and the UAW, especially as people come together to meet the country’s need for ventilators.
“As our nation struggles with the COVID-19 pandemic, volunteer UAW-GM members are doing a tremendous service for our country by volunteering to come to work to make ventilators in Kokomo,” said Terry Dittes, vice president, UAW-GM Department. “For that reason, the UAW has worked with GM to put in place stringent CDC health and safety protocols. Our goal is to make sure that each and every day, people return home to their families and communities safe and healthy. We applaud their courage in volunteering in our nation’s time of need, and we commend GM for working with the UAW to save lives across this country.”
Added Greg Wohlford, UAW Local 292 shop chairperson, “Our members responded to the call for help with courage and a desire to help America save its citizens’ lives. We have pledged, along with GM, to do everything we can to make sure that we keep these everyday heroes safe from illness and injury. The UAW is excited about working with Ventec and GM to produce ventilators in Kokomo, Indiana.”
A Phone Call Sets an Unprecedented Effort into Motion
The unprecedented teamwork that has allowed ventilator production in Kokomo to move forward so quickly began with a March 17 phone call between General Motors Chairman and CEO Mary Barra and representatives of StopTheSpread.Org, who suggested GM work with Ventec.
StopTheSpread.org was founded by Kenneth Chenault, chairman and managing director at General Catalyst and the former chief executive and chairman of American Express, and Rachel Romer Carlson, the chief executive and co-founder of Guild Education.
GM and Ventec executives had their first conference call on Wednesday, March 18 to explore how GM may be able to help Ventec increase ventilator production.
The next day, a GM team flew to Seattle to meet with the Ventec team and roll up their sleeves to help.
On Friday, March 20, GM engaged its global supply base and within 72 hours, they had developed plans to source 100 percent of the necessary parts.
The UAW’s national and local leadership embraced the project and on Wednesday, March 25, crews began preparing the Kokomo site for production.
Mass production begins in mid-April. Production will quickly scale up to 10,000 critical care ventilators or more per month.
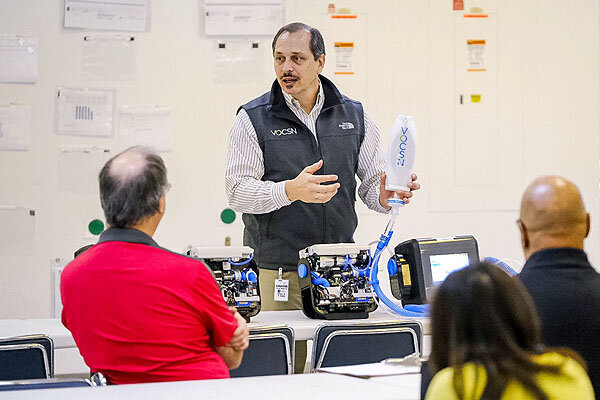
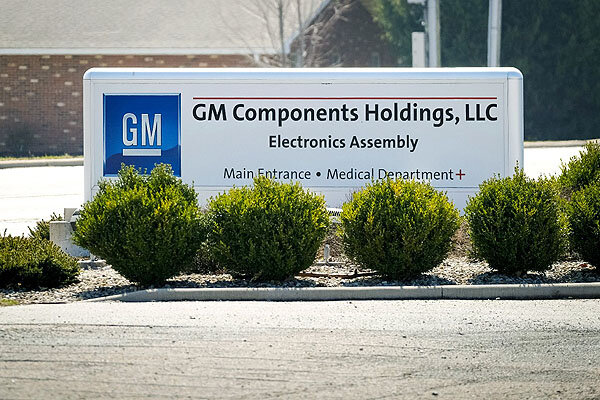
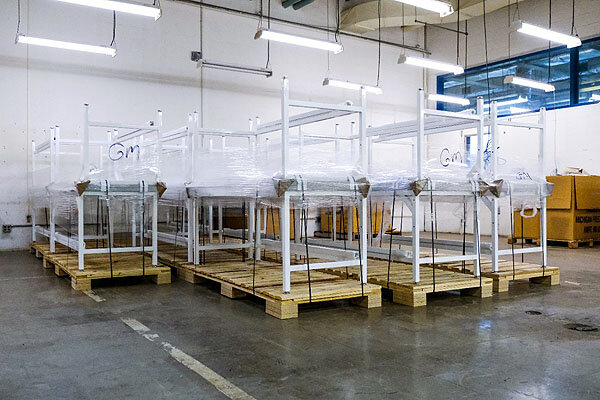
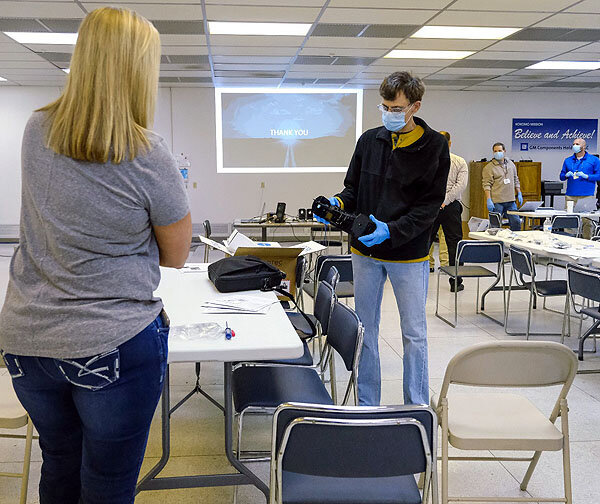
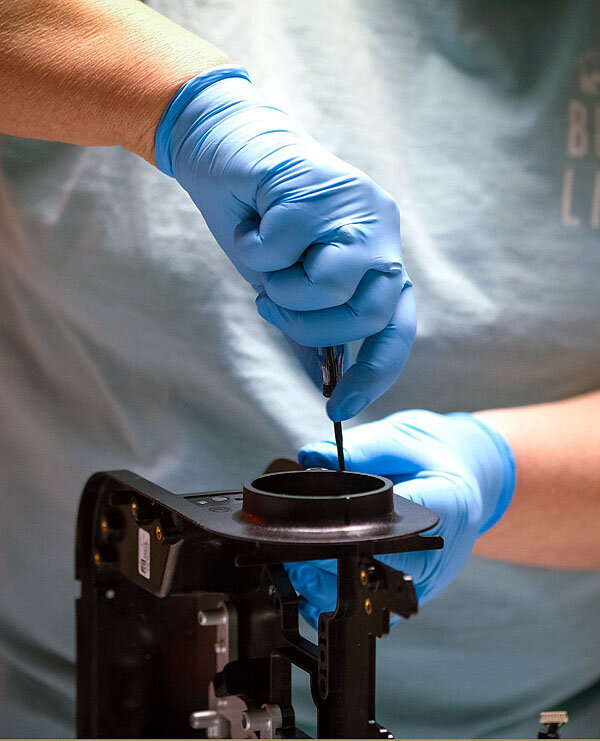
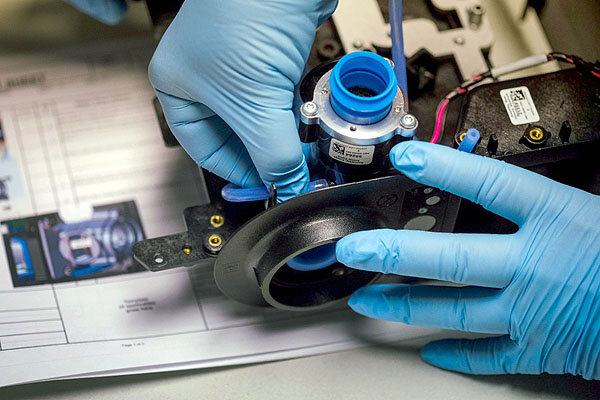
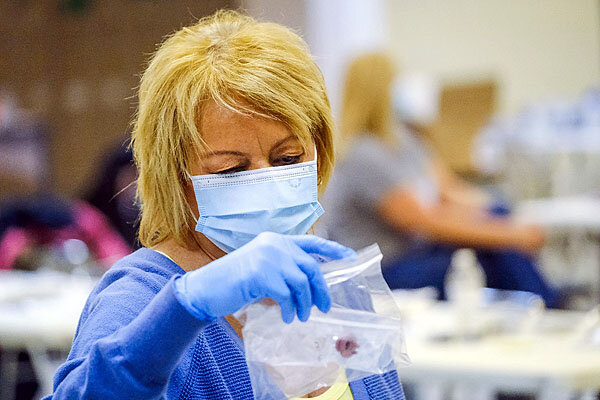
The BMW iNEXT in the hottest phase of its series development
During test drives across the desert regions of South Africa, the BMW Group’s new technology flagship masters the manifold challenges associated with extreme heat, solar radiation and dust formation on dirt tracks.
Munich. On its way to series maturity, the BMW iNEXT is completing a further chapter of its overall vehicle testing under particularly demanding conditions. Intensive test runs in the freezing cold at the polar circle are now being followed by a contrasting program in the Kalahari in Southern Africa, where in addition to extreme heat and solar radiation, permanent dust formation and off-road terrain with its sand, pebble and gravel tracks pose exceptional challenges for the BMW Group’s technology flagship. In this literally hot phase of the series development process, not only do the drive and suspension components of the BMW iNEXT, a car designed for all-electric mobility, provide proof of their functional safety, durability, and reliability, but also the car’s bodywork, interior, driver assistance systems, and digitalization technology.
The so-called hot climate tests are an integral part of both extensive and varied development and test program within the framework of the series maturity process, which entails BMW iNEXT prototypes being subjected virtually in time-lapse to the stress of an entire vehicle service life. Like every new BMW model, the vehicle’s way to serial maturity leads to the BMW Group proving ground at Miramas in Southern France, the Nürburgring Nordschleife and other racetracks and to the Winter Center in Arjeplog, Sweden, as well as to desert regions with an extremely high level of heat and dryness.
Ice track, racetrack, desert passage: A variety of tests ensures long-term driving pleasure.
With the high-speed operation, in stop & go traffic, extreme temperatures below and above zero, testing on ice and snow as well as desert sand and gravel, the pre-series vehicles master in a concentrated form all of the challenges an automobile may face in everyday traffic over a period of many years. In the process, experienced designers and efficient onboard measuring technology record the vehicle’s reactions to various weather and road surface conditions as well as other influences. This ensures that the characteristic BMW driving pleasure experienced in future production models is not impaired in any way by exceptional circumstances. Production of the series version of the BMW iNEXT will commence at the BMW Dingolfing plant in 2021. Designed as a modern Sports Activity Vehicle, the new model combines the latest innovations defined by the BMW Group in its corporate NUMBER ONE > NEXT strategy for the future fields D-ACES (Design, Autonomous, Connected, Electrified and Services). Featuring fifth-generation BMW eDrive technology, the BMW iNEXT sets new benchmarks in sportiness, efficiency, and range in a battery-powered automobile. The car’s suspension control and driver assistance systems pave the way for a further step towards autonomous driving. And current innovations in the field of operation and digitalization also underscore the future-oriented character of the BMW iNEXT.
The BMW iNEXT masters extreme stress from heat, sunlight, and dust.
The test drives through the desert and Savanna regions in the North West of South Africa offer development engineers the ideal prerequisites for testing and harmonizing all drive and suspension components under extreme conditions. Surfaces alternating between sand dunes, gravel tracks, and off-road passages pose an exceptional challenge even to the intelligent four-wheel drive system of the BMW iNEXT. In temperatures that would drain any mobile phone battery in no time at all, the integrated cooling concept for the high-voltage battery, the electric motor and the vehicle electronics of the BMW iNEXT stands the test. Moreover, the interior air conditioning, which operates by means of thermal pump technology, its control system and all further components of the vehicle electronics are subjected to the extreme conditions of the desert climate in order to prove their series maturity.
During extensive heat tests, the vehicle is repeatedly exposed to the heat of the sun for hours and later cooled down. In this way, the developers test not only the operability of the electrical systems but also the temperature stability of the materials used in the interior, because the test engineers do not accept any creaking or crackling noises even in the event of sudden and intense temperature fluctuations. Furthermore, the Kalahari offers the ideal conditions for testing the dust-tightness of flaps, doors, and bonnets. During test drives over thousands of kilometers on unpaved roads, through dune landscapes and across sandy scrublands, the BMW iNEXT is stirring up a lot of dust but without letting any of it get inside.
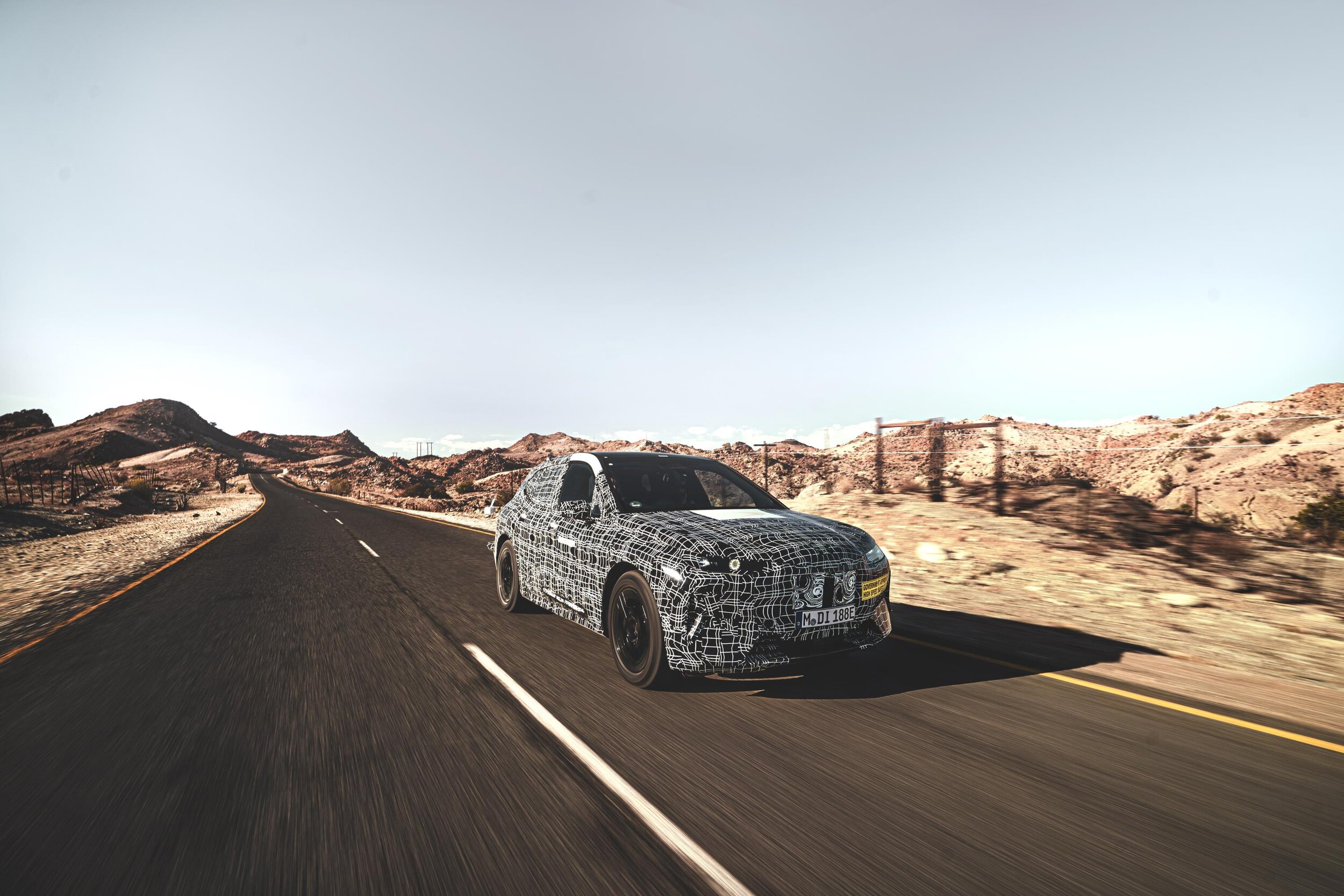
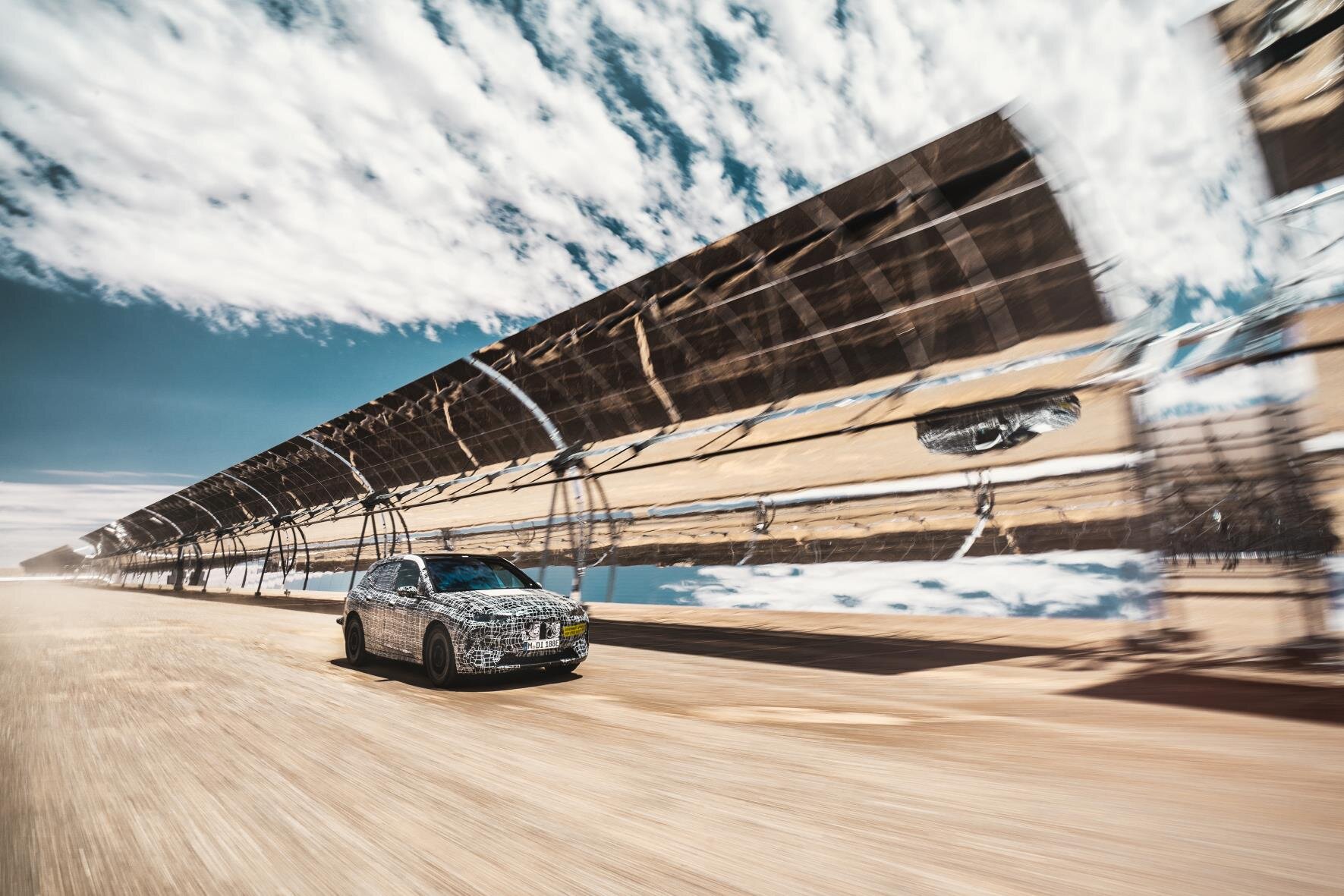
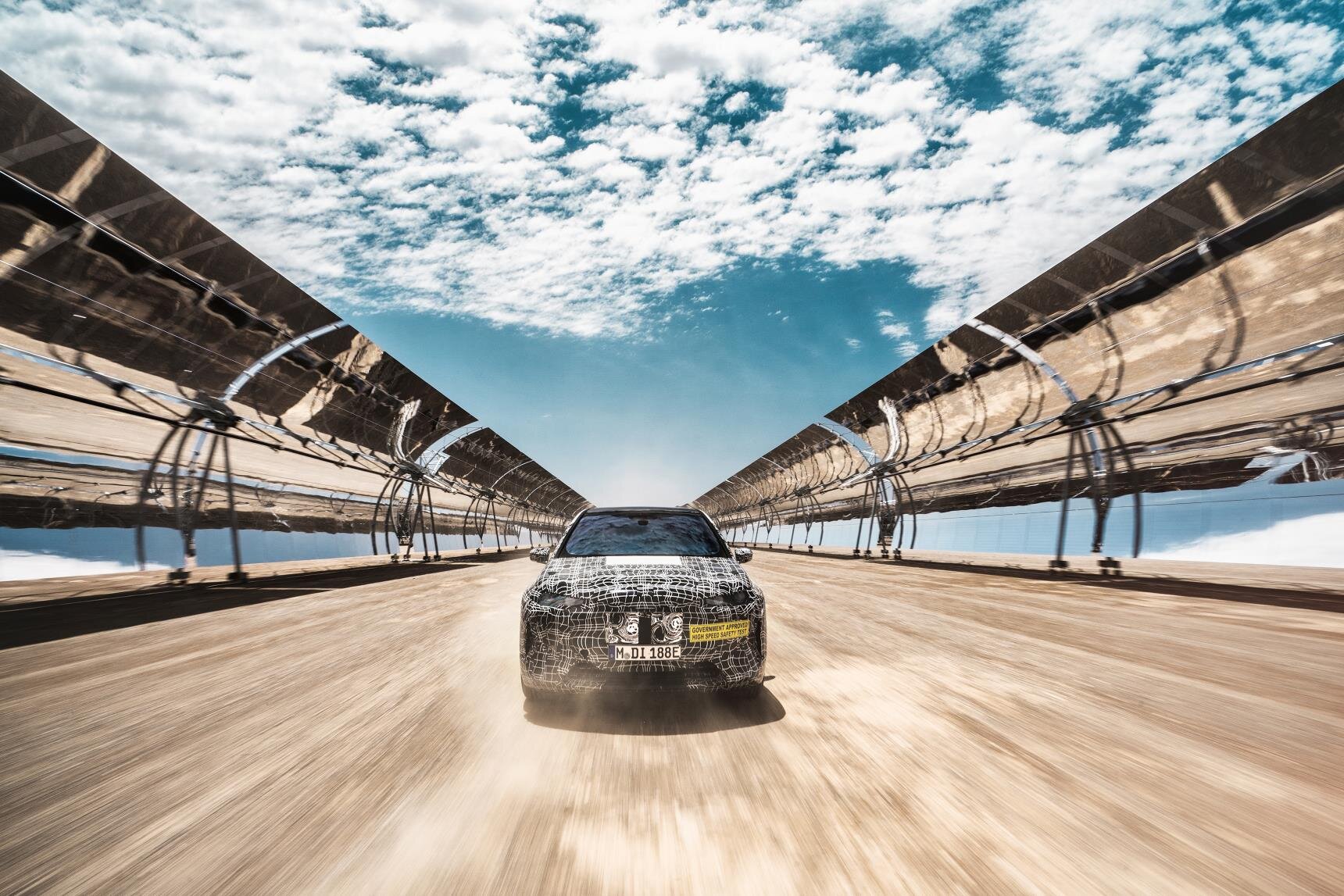
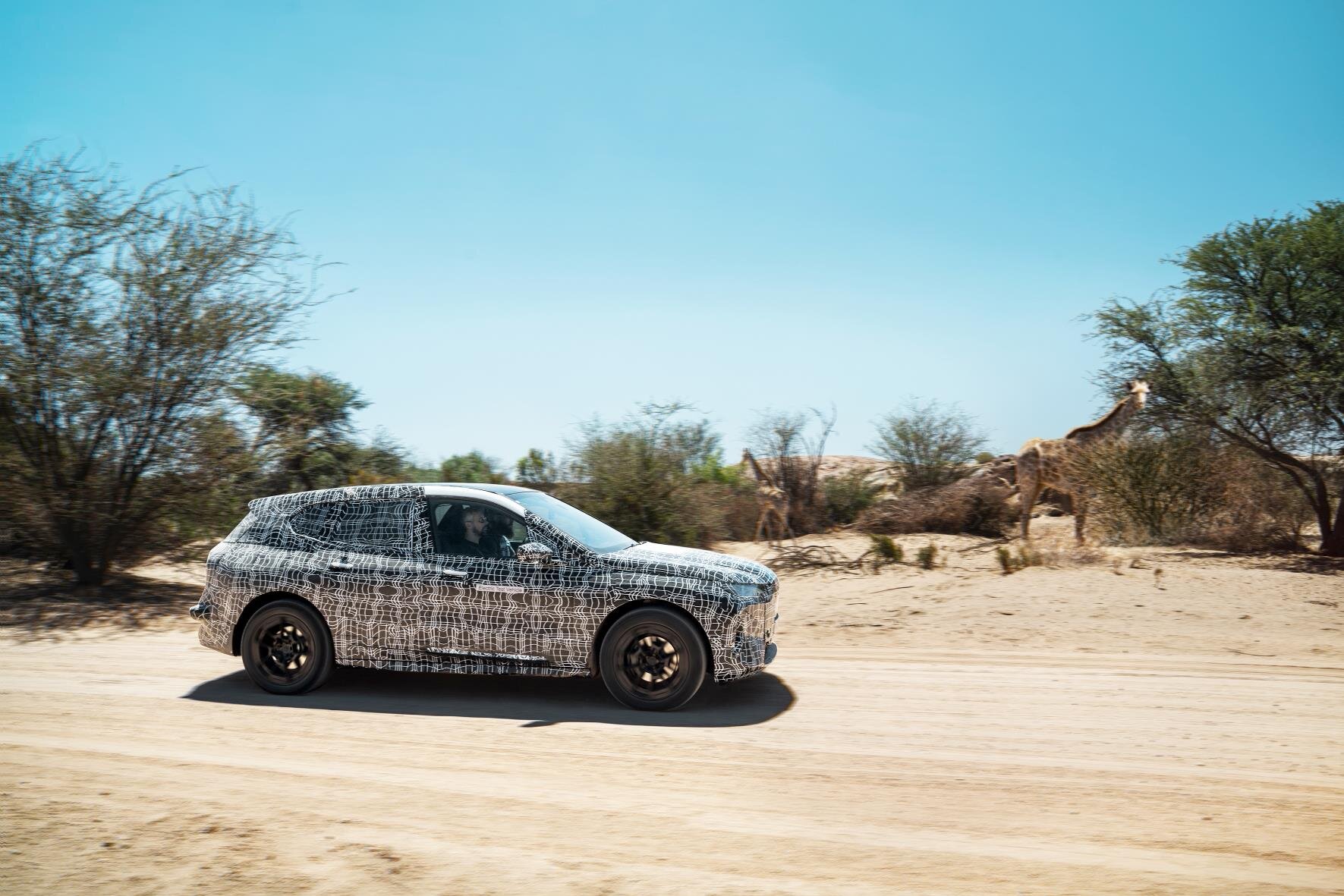
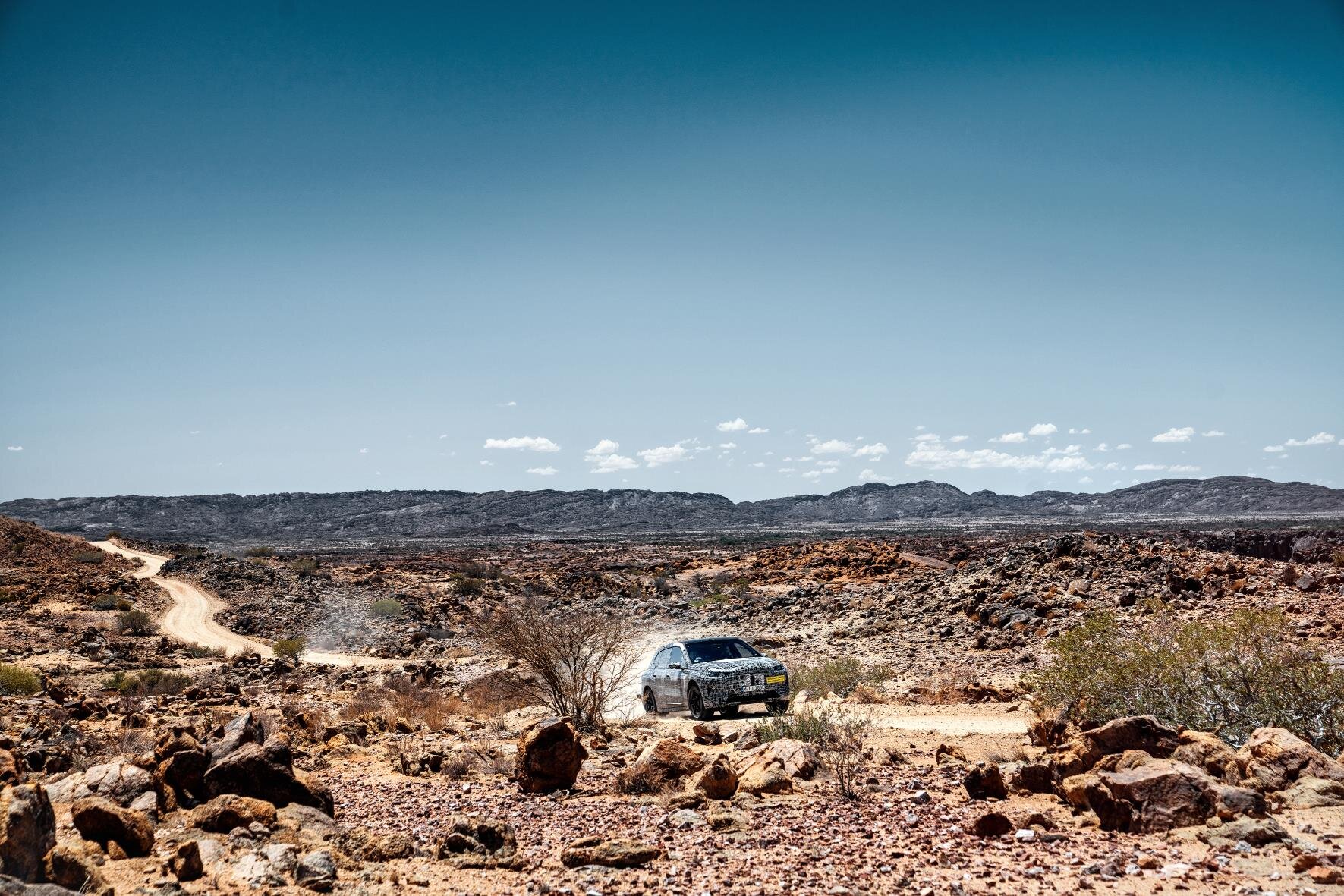
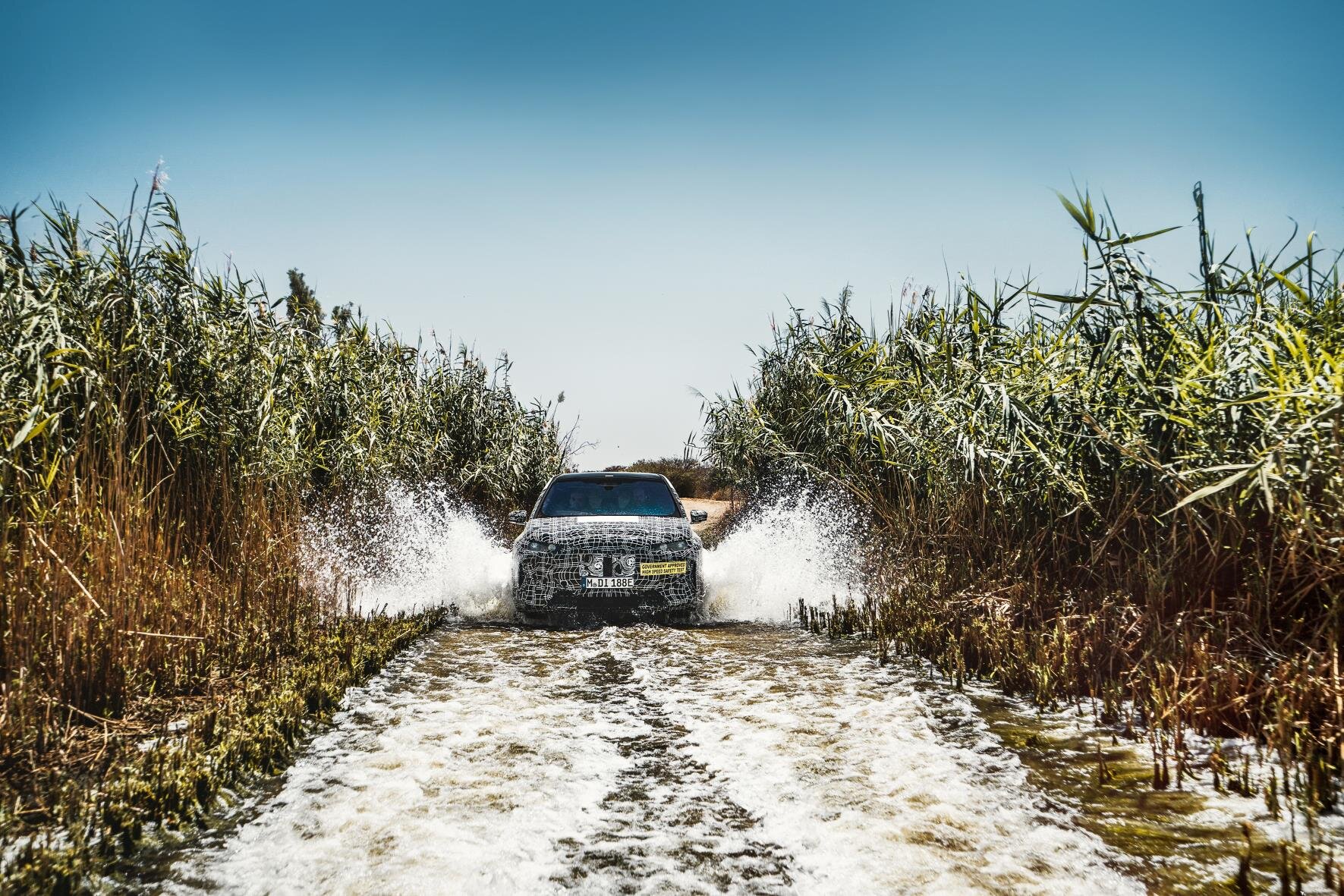
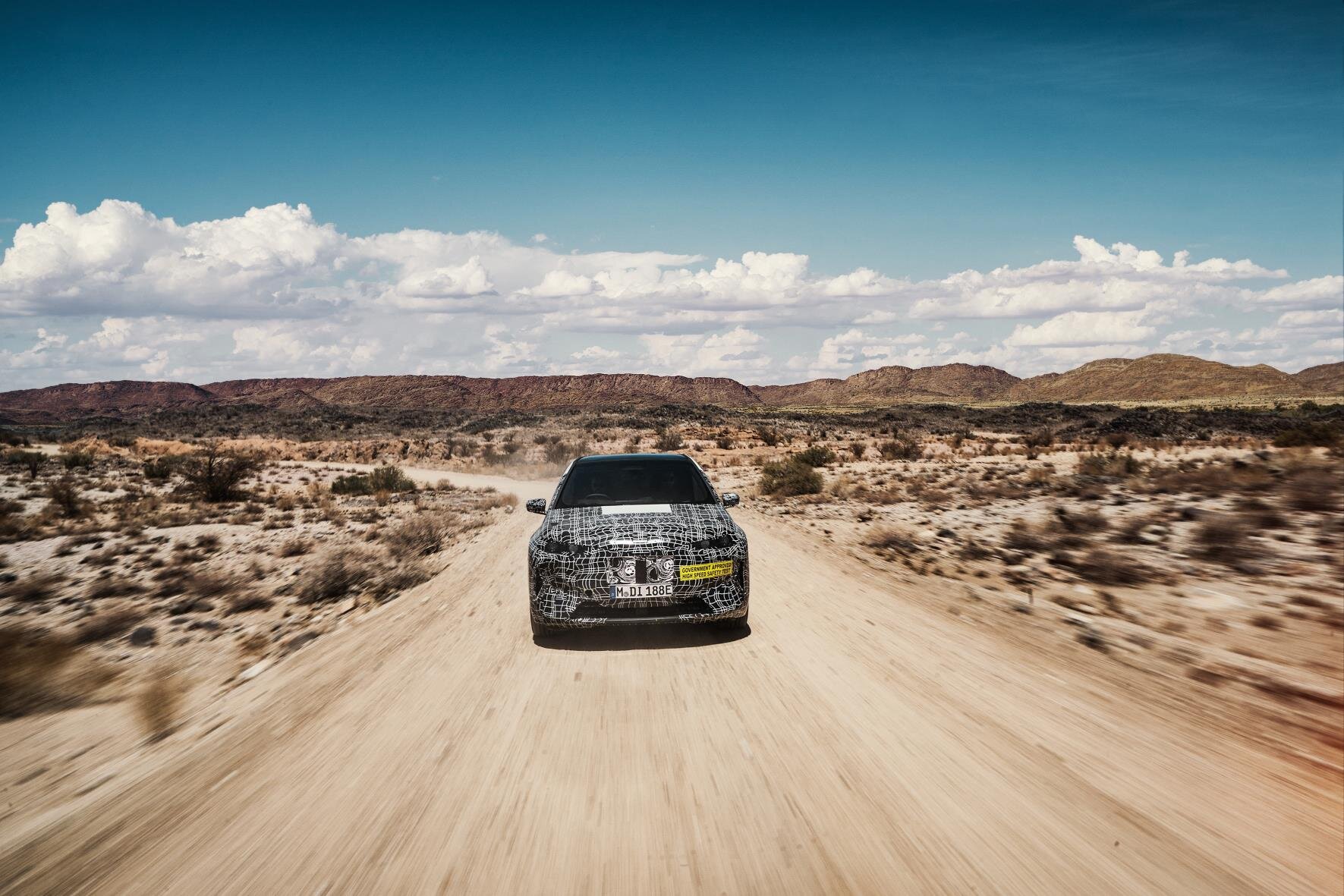
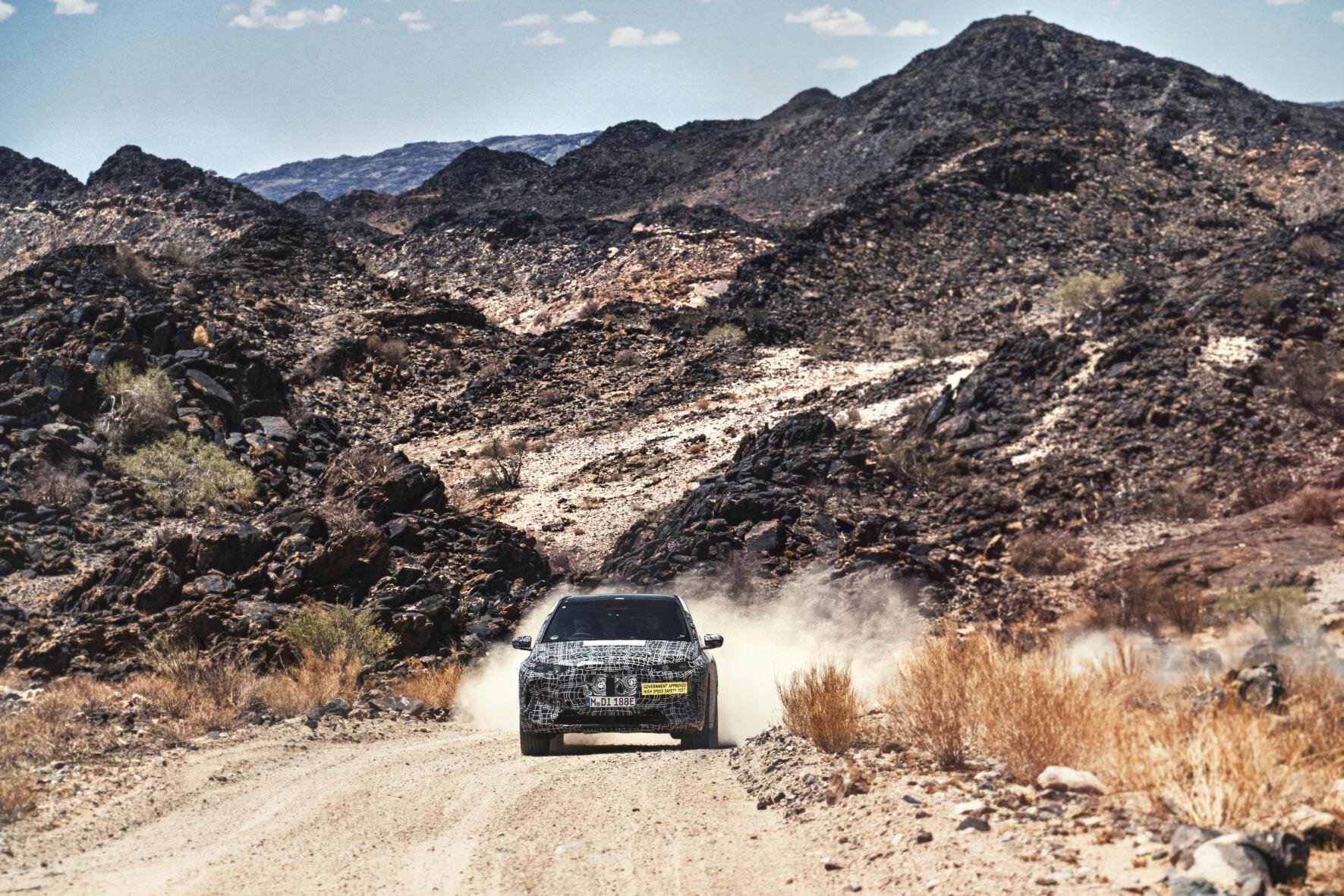
GENEVA MOTOR SHOW
GENEVA MOTOR SHOW 2020
The 2020 Geneva Motor Show has been canceled due to the coronavirus outbreak.
Below is the statement from the organizers:
The 90th edition of the GIMS, which was supposed to welcome the media from next Monday and the general public from 5 to 15 March 2020, will now finally not take place. This is in conjunction with the Federal Council of 28 February 2020 that no events with more than 1,000 people are allowed to take place until 15 March 2020. The decision falls 3 days before the opening of the exhibition to the media.
The organizers accept this decision: "We regret this situation, but the health of all participants is our and our exhibitors' top priority. This is a case of force majeure and a tremendous loss for the manufacturers who have invested massively in their presence in Geneva. However, we are convinced that they will understand this decision," said Maurice Turrettini, Chairman of the Foundation Board. We would like to warmly thank all those involved in the organization of the 2020 edition of GIMS.
A few days before the opening of the event, the construction of the stands was very nearly complete. A week ago, during the press conferences announcing the 2020 edition, there was nothing to suggest that such a measure was necessary. The situation changed with the appearance of the first confirmed coronavirus diseases in Switzerland and the injunction of the Federal Council on 28.02.2020. The event is canceled due to this decision.
In the meantime, the dismantling of the event will now have to be organized. The financial consequences for all those involved in the event are significant and will need to be assessed over the coming weeks. One thing is certain: tickets already purchased for the event will be refunded. The organizers will communicate about this as soon as possible, via their website: https://www.gims.swiss/.